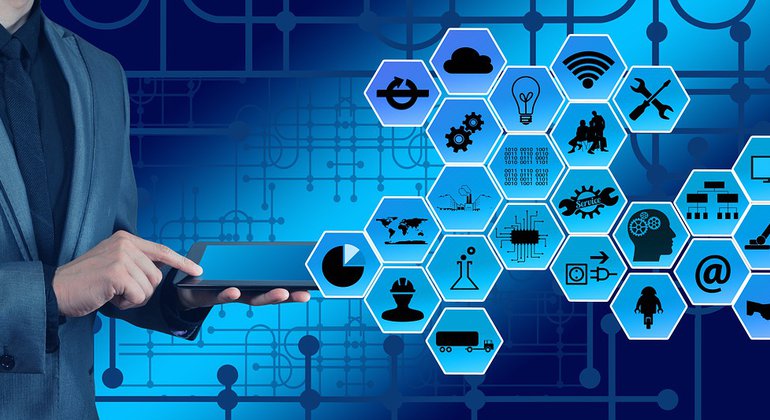
Design of a macro/mini collaborative robot using a low-impedance mini mechanism with haptic feedback capabilities
- Start: Sept. 1, 2016
- Québec
- Olympus
DESCRIPTION
Human-Robot collaboration in manufacturing environment allows leverage of both human operator capabilities such as flexibility and dexterity and of robotic systems capabilities such as speed of execution, high precision and larger payload. This project aims at developing a macro/mini Cartesian architecture which allows collaboration between human and robot for cooperative tasks. The developed robotic system should also allow haptic feedback to the operator. The robot architecture includes a conventional 3 degree-of-freedom (DoF) gantry system (macro) on which a 3 DoF passive Cartesian mechanism (mini) equipped with encoders is mounted. The mini mechanism architecture is based on the tripteron[1] robot. The end-effector of the mini mechanism is guided by the human operator while the macro mechanism is controlled by a feedback control loop using the passive Cartesian encoder information. This allows then both cooperative tasks to be performed and trajectory teaching by the human operator. Additionally, mechanical stopper installed on the mini mechanism can be used for haptic feedback to the operator. The project consists of designing and implementing control for such robot. The control system must allow 1) autonomous robot displacement, 2) collaborative displacement of the macro robot using the mini mechanism and 3) haptic feedback to the operator to simulate constraint in either real or simulated environment. Shifting between all three modes must be as continuous and intuitive as possible.