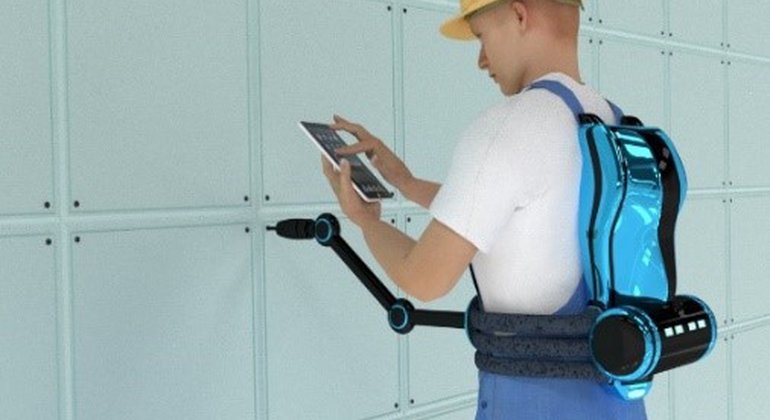
Design and manufacturing of a wearable and collaborative supplementary robotic arm based on magnetorheological clutches.
- Start: Jan. 1, 2018
- Sherbrooke
- Exonetik
DESCRIPTION
In the aerospace industry, assembly workers have to lift heavy parts and often work in non-ergonomic positions, which entail muscular fatigue, increase the risk of injuries and reduce production efficiency. Robotic systems assisting workers in their daily tasks have the potential to overcome those issues. However, industrial robotic technologies are not suitable for aerospace industry because of the weak number of planes produced and the temporary nature of the assembly process. Instead of conventional industrial robotic systems implantation, collaborative wearable robots aimed at assisting humans could be more appropriate for aerospace industry. Supernumerary robotic limbs (e.g. a second pair of arms) are wearable collaborative robots that enhance human performances and could reduce employee’s fatigue. One of the most challenging feat with collaborative robots is their interaction with human, which requires an excellent level of transparency (i.e. the ability of the robotic system to not impede the natural motion of the user interacting with the machine). In turn, this entails a combination of high force bandwidth and good back-drivability. However, current collaborative robots (e.g. exoskeletons, supernumerary robotic limb, and collaborative robots for manufacturing) suffer from a lack of transparency and a low force density. In order to overcome those issues, this PhD project aims to design and build a wearable and collaborative supernumerary robotic arm intended to help assembly workers to reduce their fatigue and increase global production efficiency. This device will be characterized by a high transparency level, a good compactness and a high force density. Finally, the wearable supernumerary robotic limb will assist workers in the following three main tasks: gravity compensation, constant force and position stabilization.