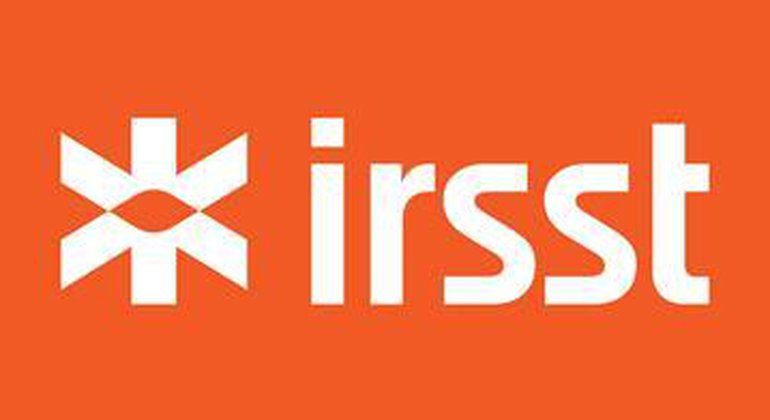
Generating safety trajectories by taking into account the piece manipulated by the collaborative robot
- Start: Jan. 1, 2018
- Montréal
- IRSST
DESCRIPTION
Human-robot cooperation continues to grow in the industry, bringing security challenges. Inspired by this new demand, several manufacturers have designed new "collaborative" robots, such as Universal Robot E-SERIES robots, OMRON TM or FANUC CR-15iA. This new generation of robots aims to eliminate physical barriers, while ensuring the safety of the operator and therefore reduce the space required for a robotic installation. Nevertheless, sharing the same space with the robot always presents risks that have to face a great challenge in terms of security. These so-called "collaborative" robots always present residual risks in certain applications, the mitigation of which involves the installation of security devices (laser scanners, or light barriers). In the ISO 10218 -1: 2011 [1], ISO 10218-2: 2011 [2] and ISO / TS 15066 [3] collaborative robotics standards, the robot's performance is restricted by imposing a reduction in speed. Or a complete shutdown when an operator enters the collaborative space.
In order to increase the efficiency of so-called "collaborative" robots in industry, the next step in human-robot collaboration is to equip robots with the ability to interact with their environments and the staff working with them. It is in this same vision that the algorithmsof trajectory planning and obstacle avoidance have emerged. Over the years, several safety constraints have been added to the choice of the optimal trajectory, in order to meet the expectations of collaborative robotics. The trajectory of a collaborative robot must be safe and the fastest to meet the high production rates in an industrial environment. In addition, the robot can change its trajectory using obstacle information to avoid collisions or receive production status to meet production demands. However, the adaptation of the trajectory decreases the predictability of the movement of the robot, thus causing a loss of concentration, fatigue and stress for the operator.
A number of collaborative applications in industry have the main operation of moving a part from point A to point B (Pick-and-Place) or feeding and unloading a machine (Machine Tending). The majority of the algorithms that generate the robot trajectories aim at securing the robot's route in relation to the effector, but fail to integrate the parameters of the manipulated part into the calculations. The trajectory is safe, but the geometric shape and orientation of the manipulated object can make the application non-collaborative in view of the standards in force.
In this project it will be question of generating safety trajectories by taking into account the piece manipulated by the collaborative robot (Cobot), while avoiding obstacles and the operator. Several algorithms for the day in the field of trajectory optimization (A *, RRT or Rapidly-exploring Random Tree, Genetic Algorithm, etc.), one or more will be used and optimized for application in an industrial environment and to suit a collaborative application.